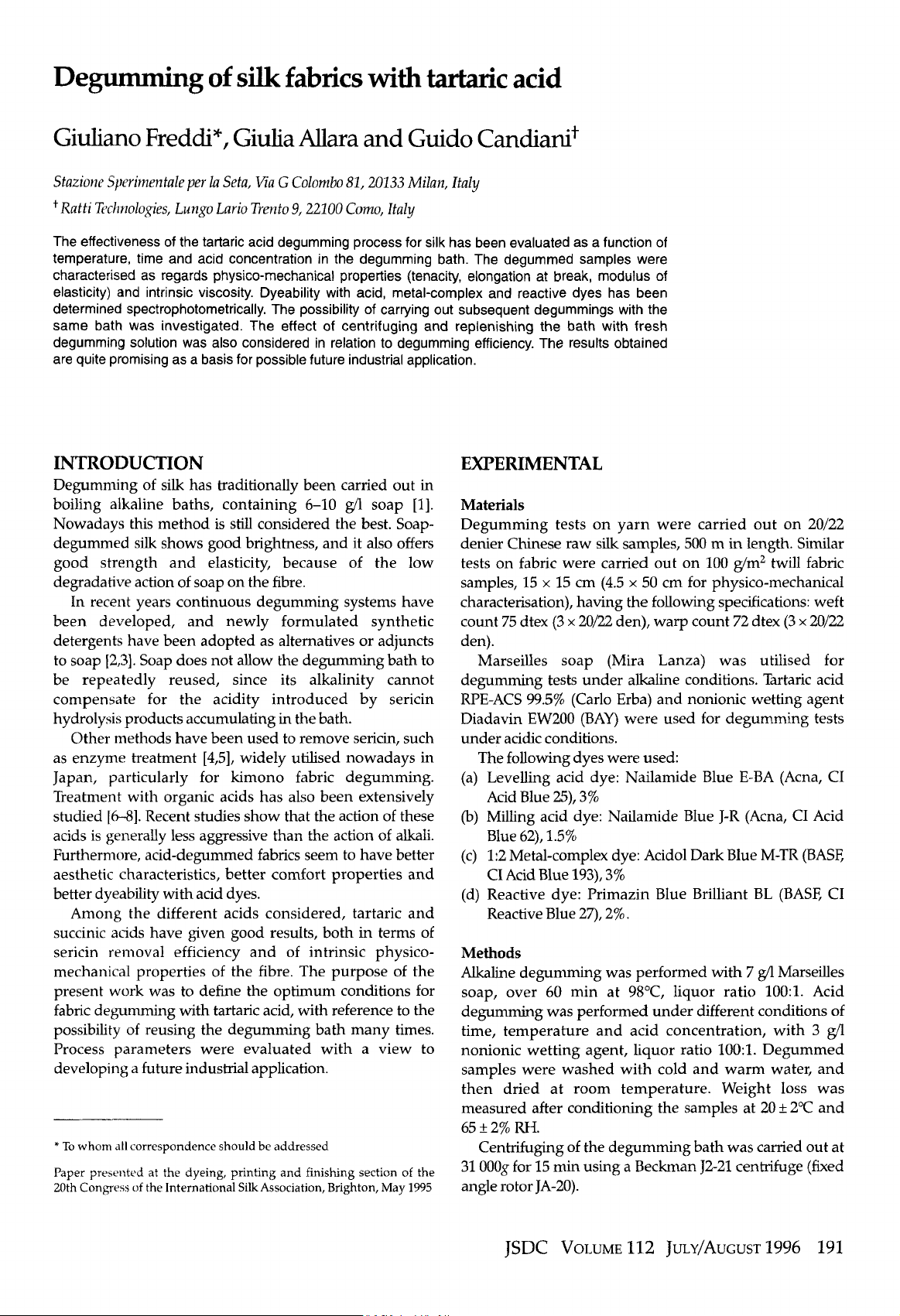
Degumming
of
silk
fabrics
with
tartaric
acid
Giuhano Freddi", Giulia Allara and Guido Candianit
Stazionr Sprimentale per
la
Seta,
Via
G
Colombo 81,20133 Milan,
Italy
Ratti
Echnologies,
Lung0 Lario Trento 9,22100
Corno,
ltaly
The effectiveness
of
the tartaric acid degumming process for silk has been evaluated as a function of
temperature, time and acid concentration in the degumming bath. The degummed samples were
characterised as regards physico-mechanical properties (tenacity, elongation at break, modulus
of
elasticity) and intrinsic viscosity. Dyeability with acid, metal-complex and reactive dyes has been
determined spectrophotometrically. The possibility of carrying
out
subsequent degummings with the
same bath was investigated. The effect of centrifuging and replenishing the bath with fresh
degumming solution was also considered in relation
to
degumming efficiency. The results obtained
are quite promising as a basis for possible future industrial application.
INTRODUCTION
Degumming of silk has traditionally been carried out in
boiling alkaline baths, containing 6-10
g/l
soap [l].
Nowadays this method is
still
considered the best. Soap-
degummed
silk
shows good brightness, and it also offers
good strength and elasticity, because of the low
degradative action of soap on the fibre.
In recent years continuous degumming systems have
been developed, and newly formulated synthetic
detergents have been adopted as alternatives or adjuncts
to soap
[2,3].
Soap does not allow the degumming bath to
be repeatedly reused, since its alkalinity cannot
compensate for the acidity introduced by sericin
hydrolysis products accumulating in the bath.
Other methods have been used to remove sericin, such
as enzyme treatment [4,5], widely utilised nowadays in
Japan, particularly for kimono fabric degumming.
Treatment with organic acids has also been extensively
studied 16-81. Recent studies show that the action of these
acids is generally less aggressive than the action of alkali.
Furthermore, acid-degummed fabrics seem to have better
aesthetic characteristics, better comfort properties and
better dyeabihty with acid dyes.
Among the different acids considered, tartaric and
succinic acids have given good results, both in terms of
sericin removal efficiency and of intrinsic physico-
mechanical properties of the fibre. The purpose of the
present work was to define the optimum conditions for
fabric degumming with tartaric acid, with reference to the
possibility of reusing the degumming bath many times.
Process pdrameters were evaluated with a view to
developing
a
future industrial application.
*
To
whom
all
correspondence
should
be addressed
Paper prrsrntcd at the dyeing, printing and finishing section
of
the
20th Conge55
of
the Internahonal Silk Association, Brighton, May
1995
EXPERIMENTAL
Materials
Degumming tests on yarn were carried out on 20/22
denier Chinese raw
siLk
samples, 500 m
in
length. Similar
tests on fabric were carried out on 100 g/m2 twill fabric
samples, 15
x
15 cm (4.5
x
50
cm for physico-mechanical
characterisation), having
the
following specifications: weft
count 75 dtex (3
x
20/22 den), warp count 72 dtex
(3
x
20/22
den).
Marseilles soap (Mira Lanza) was utilised for
degumming tests under alkaline conditions. Tartaric acid
WE-ACS 99.5% (Carlo Erba) and nonionic wetting agent
Diadavin
EW200
(BAY)
were used for degumming tests
under acidic conditions.
(a) Levelling acid dye: Nailamide Blue E-BA (Acna,
CI
(b)
Milling acid dye: Nailamide Blue
J-R
(Acna, CI Acid
(c) 1:2 Metal-complex dye: Acidol Dark Blue M-TR (BASE
(d) Reactive dye: Primazin Blue Brilliant
BL
(BASE
CI
The following dyes were used:
Acid Blue
25),
3%
Blue 62), 1.5%
CI Acid Blue 193),
3%
Reactive Blue 27),2%.
Methods
Alkaline degumming was performed with
7
g/l
Marseilles
soap, over 60 min at 98"C, liquor ratio 1OO:l. Acid
degumming was performed under different conditions of
time, temperature and acid concentration, with
3
g/l
nonionic wetting agent, liquor ratio
1OO:l.
Degummed
samples were washed with cold and warm water, and
then dried at room temperature. Weight loss was
measured after conditioning the samples at
20
k
2°C and
65
f
2%
RH.
Centrifuging of the degumming bath was carried out at
31
0008
for
15
min
using
a Beckman J2-21 centrifuge (fixed
angle rotor
JA-20).
JSDC
VOLUME
112
JULY/AUGUST
1996
191